Porosity in Welding: Identifying Common Issues and Implementing Ideal Practices for Avoidance
Porosity in welding is a pervasive issue that typically goes unnoticed up until it causes considerable problems with the stability of welds. In this conversation, we will certainly check out the key factors contributing to porosity development, examine its harmful impacts on weld efficiency, and go over the finest techniques that can be taken on to reduce porosity incident in welding procedures.
Typical Reasons of Porosity
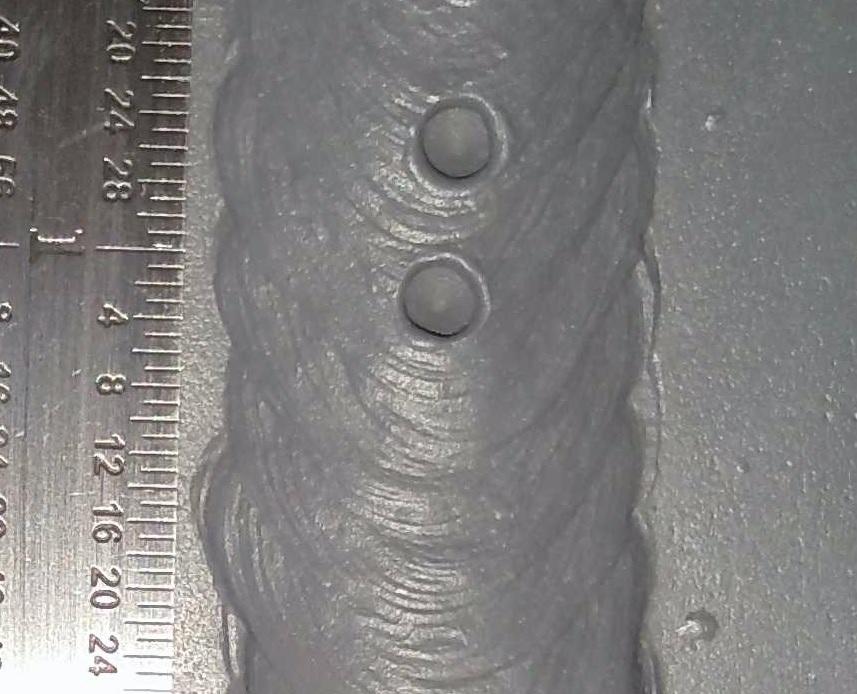
Utilizing unclean or wet filler materials can present pollutants right into the weld, adding to porosity problems. To mitigate these typical causes of porosity, comprehensive cleaning of base metals, proper shielding gas selection, and adherence to optimal welding specifications are vital practices in achieving top notch, porosity-free welds.
Effect of Porosity on Weld Quality

The visibility of porosity in welding can significantly jeopardize the structural honesty and mechanical buildings of bonded joints. Porosity produces voids within the weld metal, weakening its general toughness and load-bearing capability.
Welds with high porosity levels tend to show lower effect toughness and decreased ability to warp plastically prior to fracturing. Porosity can hinder the weld's ability to successfully send forces, leading to early weld failing and possible safety dangers in essential structures.
Ideal Practices for Porosity Prevention
To boost the architectural integrity and quality of welded joints, what details actions can be executed to decrease the incident of porosity during the welding process? Making use address of the right welding strategy for the specific product being welded, such as readjusting the welding angle and weapon setting, can even more protect against porosity. Routine assessment of welds and immediate removal of any problems determined throughout the welding process are necessary practices to stop porosity and produce top notch welds.
Importance of Correct Welding Methods
Implementing correct welding strategies is paramount in making certain the structural stability and quality of bonded joints, constructing upon the structure of effective porosity avoidance measures. Welding strategies straight influence the total toughness and durability of the welded framework. One essential element of proper welding techniques is keeping the right warm input. Excessive warmth can bring about increased porosity due to the entrapment of gases in the weld swimming pool. On the other hand, not enough heat may lead to insufficient combination, developing prospective weak points in the joint. Additionally, using the appropriate welding criteria, such as voltage, present, and take a trip rate, is important for attaining audio welds with marginal porosity.
In addition, the option of welding process, whether it be MIG, TIG, or stick welding, must align with the specific requirements of the project to guarantee ideal outcomes. Proper cleaning and preparation of the base metal, in addition to selecting the right filler material, are likewise important elements of competent welding techniques. By adhering to these finest techniques, welders can minimize the threat of porosity development and create top notch, structurally audio welds.
Examining and Top Quality Control Procedures
Quality assurance measures play an essential function in validating the integrity and reliability of welded joints. Testing treatments are vital to discover and protect against porosity in welding, making sure the toughness and resilience of the final item. Non-destructive screening methods such as ultrasonic screening, radiographic screening, and visual assessment are frequently employed to recognize prospective problems like porosity. These techniques enable the assessment of weld high quality without compromising the stability of the joint. What is Porosity.
Post-weld examinations, on the you could check here other hand, evaluate the last weld for any type of flaws, consisting of porosity, and validate that it meets specified requirements. Executing a thorough quality control plan that includes complete screening treatments and inspections is extremely important to minimizing porosity problems and making certain the general top quality of welded joints.
Verdict
To conclude, porosity in welding can be a typical concern that affects the quality of welds. By recognizing the common root causes of porosity and carrying out finest methods for prevention, such as appropriate welding methods and screening steps, welders can guarantee excellent quality and trustworthy welds. It is vital to focus on prevention methods to minimize the incident of visit porosity and keep the stability of welded structures.